The Future of Construction: Understanding Prefabricated Building
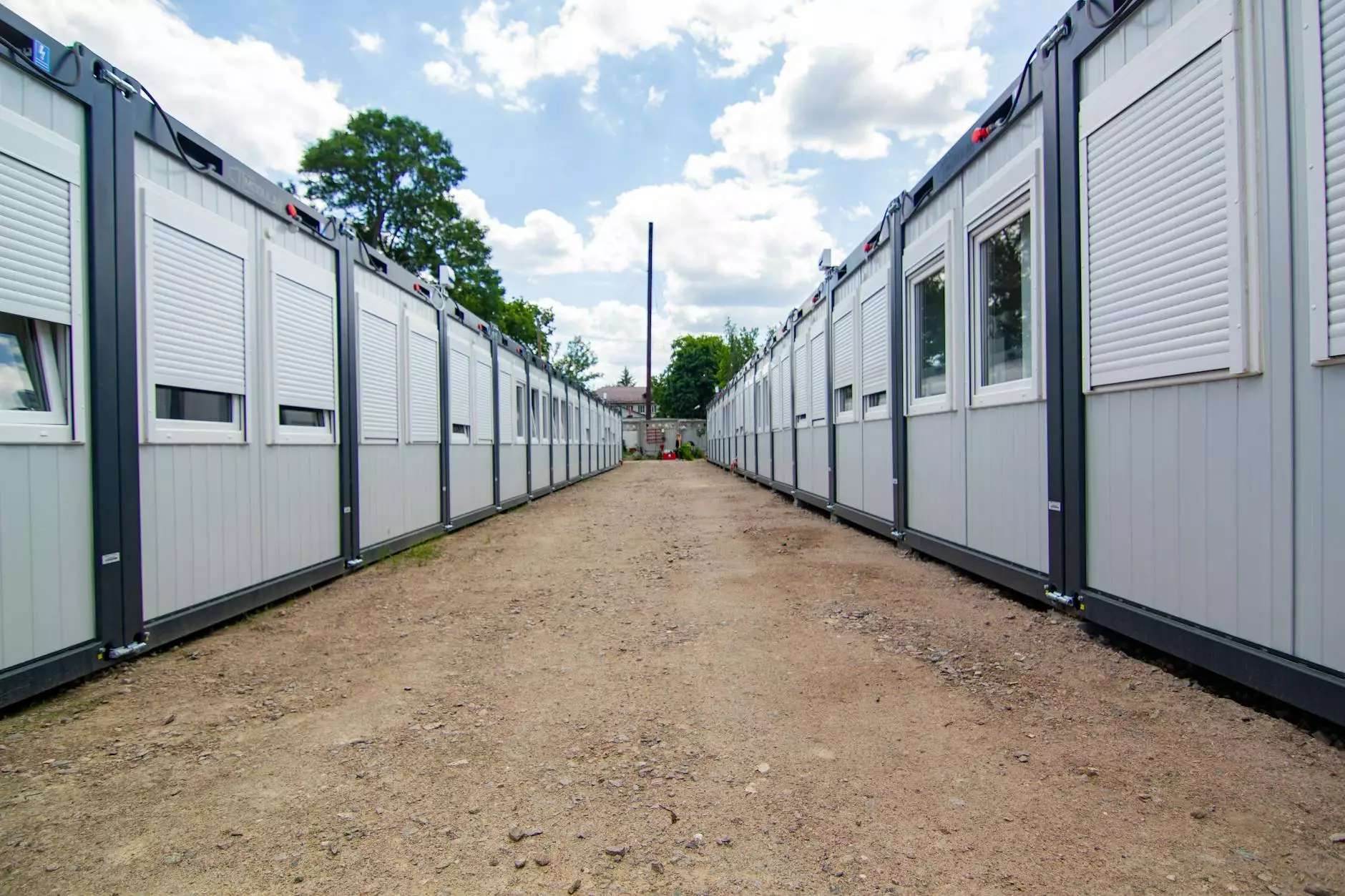
In today’s fast-paced world, where time is money and efficiency is key, the construction industry is undergoing a significant transformation. One of the most impactful methods emerging in this landscape is the concept of prefabricated building. This innovative approach to construction not only optimizes time but also enhances quality, reduces waste, and offers a sustainable solution to meet the demands of modern architecture.
What is Prefabricated Building?
Prefabricated building refers to the process of assembling standard building components, such as walls, roofs, and floors, in a factory setting before transporting them to the construction site for assembly. This method contrasts sharply with traditional construction, where most building processes occur onsite. By manufacturing components in a controlled environment, builders can ensure higher accuracy and quality, while minimizing the risk of weather-related delays.
Key Advantages of Prefabricated Building
Embracing the modular method of construction offers numerous advantages, which include:
- Faster Construction Time: Prefabrication allows for simultaneous construction processes, reducing the overall building timeline significantly.
- Cost Efficiency: Lower labor costs and reduced waste contribute to overall savings in a construction project.
- Higher Quality Control: Components are manufactured in a factory setting, allowing for stricter quality control and precision.
- Reduced Waste: Prefabricated construction processes generate less waste, contributing to more sustainable building practices.
- Design Flexibility: Components can be customized based on the specific needs of a project, allowing for creative architectural designs.
The Process of Prefabricated Building
Understanding the process behind prefabricated building provides insight into how this method functions efficiently. The typical process can be broken down into several key phases:
1. Design and Engineering
The journey begins with careful design and engineering. Using advanced software, architects and engineers collaborate to create detailed blueprints that specify dimensions, materials, and structural requirements. This design phase is crucial, as it lays the foundation for the entire project.
2. Component Manufacturing
Once the design is finalized, the production process begins in a factory environment. Here, prefabricated components are manufactured under controlled conditions. This step allows for seamless integration of utilities, such as electrical and plumbing systems, before they are transported to the construction site.
3. Site Preparation
While components are being manufactured, the construction site is simultaneously prepared. This includes grading the land, laying foundations, and ensuring that all necessary permits are in place. The parallel nature of these processes contributes to the efficiency of prefabricated building.
4. Delivery and Assembly
Once the components are complete, they are transported to the construction site. Skilled teams work to assemble these modules quickly and accurately, resulting in a fully functional structure in a fraction of the time required for traditional methods.
Applications of Prefabricated Building
The versatility of prefabricated buildings allows them to be used across various sectors, including:
- Residential Homes: Many modern homes are being built using prefabricated materials, providing homeowners with customizable options while maintaining efficiency.
- Commercial Properties: From office buildings to retail spaces, prefabricated structures are ideal for rapid deployment and scaling business operations.
- Institutional Buildings: Schools, hospitals, and other civic structures utilize prefabrication to meet urgent demand while adhering to strict regulations.
- Temporary Structures: Event spaces, site offices, and emergency shelters benefit from quick installation and dismantling of prefabricated units.
Sustainability in Prefabricated Building
In an era where sustainability is paramount, prefabricated building stands out as an environmentally friendly construction method. The reduced waste generated during the manufacturing phase, along with energy-efficient designs, contribute to a lower carbon footprint. Furthermore, many prefabricated components can utilize sustainable materials, making it easier to create environmentally responsible structures.
Challenges and Considerations
While prefabricated buildings offer numerous benefits, there are challenges and considerations to be aware of:
- Transportation Costs: The cost and logistics of transporting large components can be significant, especially in remote areas.
- Local Regulations: Compliance with local building regulations can be more complex due to the modular nature of prefabricated structures.
- Design Limitations: Although customization is available, some constraints may exist based on the prefabrication process.
The Future of Prefabricated Building
The future prospects for prefabricated building are exceptionally bright. As technology advances, expect innovations that will further enhance efficiency, sustainability, and design possibilities. Incorporating smart technologies and green building practices will likely become standard in new prefabricated constructions.
Conclusion
In conclusion, prefabricated building represents a revolutionary approach in the construction industry. By focusing on efficiency, quality, and sustainability, this method addresses many of the pressing challenges faced in traditional construction. As more contractors and building supply companies, like Module-T, recognize the benefits of this innovative approach, the adoption of prefabricated structures will undoubtedly continue to grow. Embracing this change not only paves the way for faster project completion but also supports a more sustainable future for construction. Together, we can build a smarter, greener world one prefabricated unit at a time.
For contractors and those involved in building supplies, understanding and implementing prefabricated building methods can significantly bolster your business's competitive edge. Embrace the future of construction today!