Understanding Precision Mold in Metal Fabrication
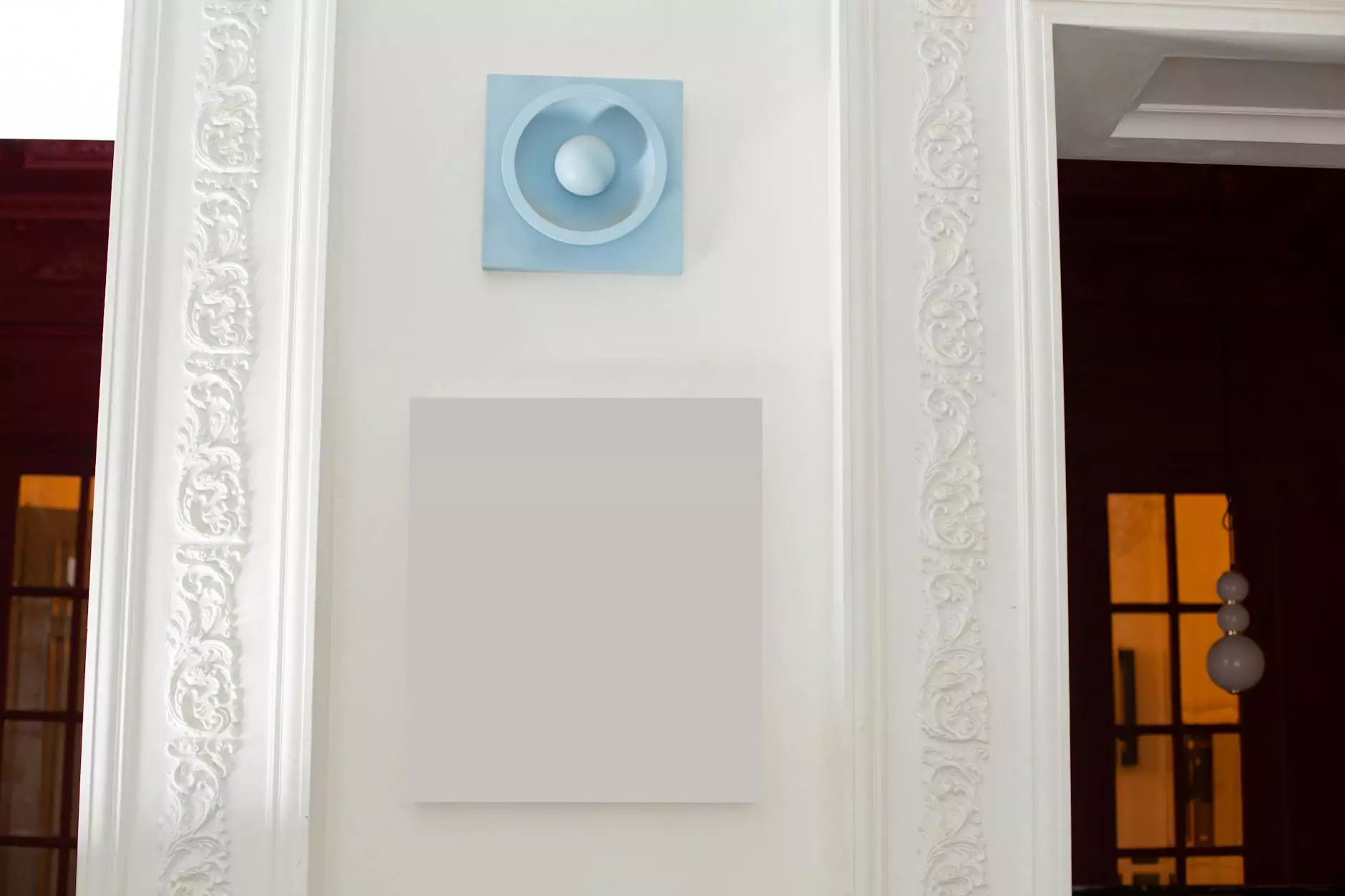
Precision mold technology is a fundamental aspect of modern manufacturing, particularly within the realm of metal fabrication. It plays a critical role in ensuring that products are not only created efficiently but also meet the stringent quality requirements of today’s marketplace. The ability to produce high-quality components with exact dimensions is a necessity in many industries, including automotive, aerospace, and consumer electronics.
The Significance of Precision Molds
In the dynamic landscape of manufacturing, precision molds represent a convergence of technology and art. These molds are engineered to create components with unmatched accuracy and repeatability. The significance of precision molds can be understood through several key benefits:
1. Enhanced Quality Control
One of the primary advantages of utilizing precision molds is their impact on quality control. The precision with which these molds are made allows manufacturers to produce components that conform to exact specifications. This means that the finished products are often significantly higher in quality, reducing defects and the need for rework.
2. Increased Efficiency
Efficiency is crucial in any manufacturing process. Precision molds enable faster production cycles as they can produce multiple parts in a single operation. This not only speeds up the manufacturing process but also contributes to lower labor costs and reduced operational expenses. The high level of repeatability means less downtime for adjustments and calibrations, allowing for uninterrupted production.
3. Cost-Effectiveness
While the initial investment in precision mold technology may be substantial, the long-term cost savings are significant. High-quality molds lead to less material waste, fewer defective parts, and a more streamlined production line. Moreover, the longevity of precision molds means that manufacturers can see a considerable return on their investment over time.
4. Design Flexibility
Modern precision molds allow for a wide range of designs and customizations that were previously difficult to achieve. This flexibility opens the door to innovative product designs, as manufacturers can explore new shapes and features without the inherent limitations of traditional mold-making processes.
How Precision Molds are Made
The process of creating precision molds involves several sophisticated techniques and high-end technology. Below is an overview of the stages involved in mold-making:
1. Design and Engineering
The mold-making process begins with detailed design and engineering, utilizing CAD software. This stage involves input from various stakeholders to ensure that the mold will meet all necessary specifications and functional requirements.
2. Material Selection
Choosing the right materials is crucial for precision molds. Common materials include steel and aluminum, each providing different advantages depending on the purpose of the mold and the desired lifespan. Steel molds are typically favored for their durability, while aluminum molds can be beneficial for short-run production due to their lighter weight and quicker turnaround times.
3. CNC Machining
Once the design is finalized and materials are selected, CNC (Computer Numerical Control) machining is employed for high-precision cuttings. This process allows for the creation of intricate details with exacting accuracy, which is essential for precise applications.
4. Finishing Processes
The finished molds often undergo several finishing processes to enhance their surface quality. Processes such as polishing, coating, and heat treatment may be applied to ensure optimal performance and longevity of the mold.
Applications of Precision Molds in Various Industries
Precision molds are utilized across various sectors, each with unique requirements and applications. Here’s a closer look at some of the key industries leveraging this technology:
1. Automotive Industry
The automotive industry relies heavily on precision molds for producing components such as brackets, housings, and panels. These parts must meet precise specifications to ensure compatibility and safety in vehicle assembly. The use of precision molds allows manufacturers to achieve this level of accuracy while maintaining high production rates.
2. Aerospace Industry
Aerospace applications demand the highest standards of quality and precision due to safety considerations. Precision molds enable the production of intricate components such as turbine blades and structural supports. The ability to create parts with minimal weight and maximum strength is essential for modern aircraft.
3. Consumer Electronics
In the consumer electronics realm, precision molds are critical for producing small, intricate parts that are integral to devices such as smartphones, laptops, and wearables. The demand for lightweight, durable, and aesthetically pleasing components is met through advanced mold technology.
Challenges in Precision Mold Manufacturing
Despite the numerous advantages of precision molds, manufacturers face several challenges that must be managed effectively. Here are some of the common obstacles encountered:
- High Initial Costs: Investing in precision mold technology can require significant capital, which may be a barrier for smaller manufacturers.
- Skill Requirement: The operation of CNC machines and mold-making processes demands a skilled workforce, and finding qualified personnel can be challenging.
- Maintenance and Repairs: While precision molds are designed for longevity, they still require regular maintenance and potential repairs that can lead to downtime.
Future Trends in Precision Mold Technology
The future of precision mold technology is bright, with several emerging trends poised to reshape the industry:
1. Integration of AI and Automation
Artificial intelligence is set to play a significant role in optimizing mold design and manufacturing processes. Automation will enhance production efficiency and accuracy, further reducing the likelihood of human error.
2. Sustainable Manufacturing Practices
As industries move toward sustainable practices, the mold-making process is also adapting. The use of eco-friendly materials and processes that minimize waste will become increasingly important.
3. Advances in Material Science
Ongoing research in material science is leading to the development of new mold materials that offer enhanced properties, such as greater durability and resistance to corrosion, further extending the life and effectiveness of precision molds.
Conclusion
In conclusion, the role of precision mold technology in metal fabrication cannot be overstated. It enhances product quality, increases efficiency, and reduces costs across various industries. As manufacturing continues to evolve, embracing advancements in technology and materials will further optimize the benefits derived from precision molds. Companies like those found at deepmould.net are at the forefront of these changes, ensuring they remain competitive in an ever-demanding market.